Bills Of Material parameters are setup for each inventory organization. It controls some basic behaviour of BOM module.
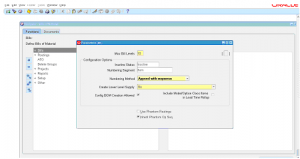
Navigate to BOM responsibility –> Setup –> Bills Of Material Parameters.
1 ) Max Bill Levels: This limits the number of levels BOM can be setup
2 ) Inactive status: To make any Item/BOM inactive we need select the appropriate status code that is used for inactive. These status codes are defined as setup and attached to Items.
3 ) Numbering Segment: Used when creating configuring items. Usually it is ITEM.
4 ) Numbering method: You can set automatic or user defined numbering method. Different values you can set are
Append Sequence
Replace with sequence
Replace with Order, Line number
User Defined
5 ) Create Lower Level Supply: Select YES or NO.
6 ) Config BOM Creation allowed: Check or uncheck. Usually check this in manufacturing orgs where the config BOM must exists to manufacture that assembly.
7 ) Inlcude Model/Option class items in lead time rollup: Check to roll up the lead times.
8 ) Check or uncheck ‘Use Phantom Routings
9 ) Check or uncheck Inherit phantom Operation sequence